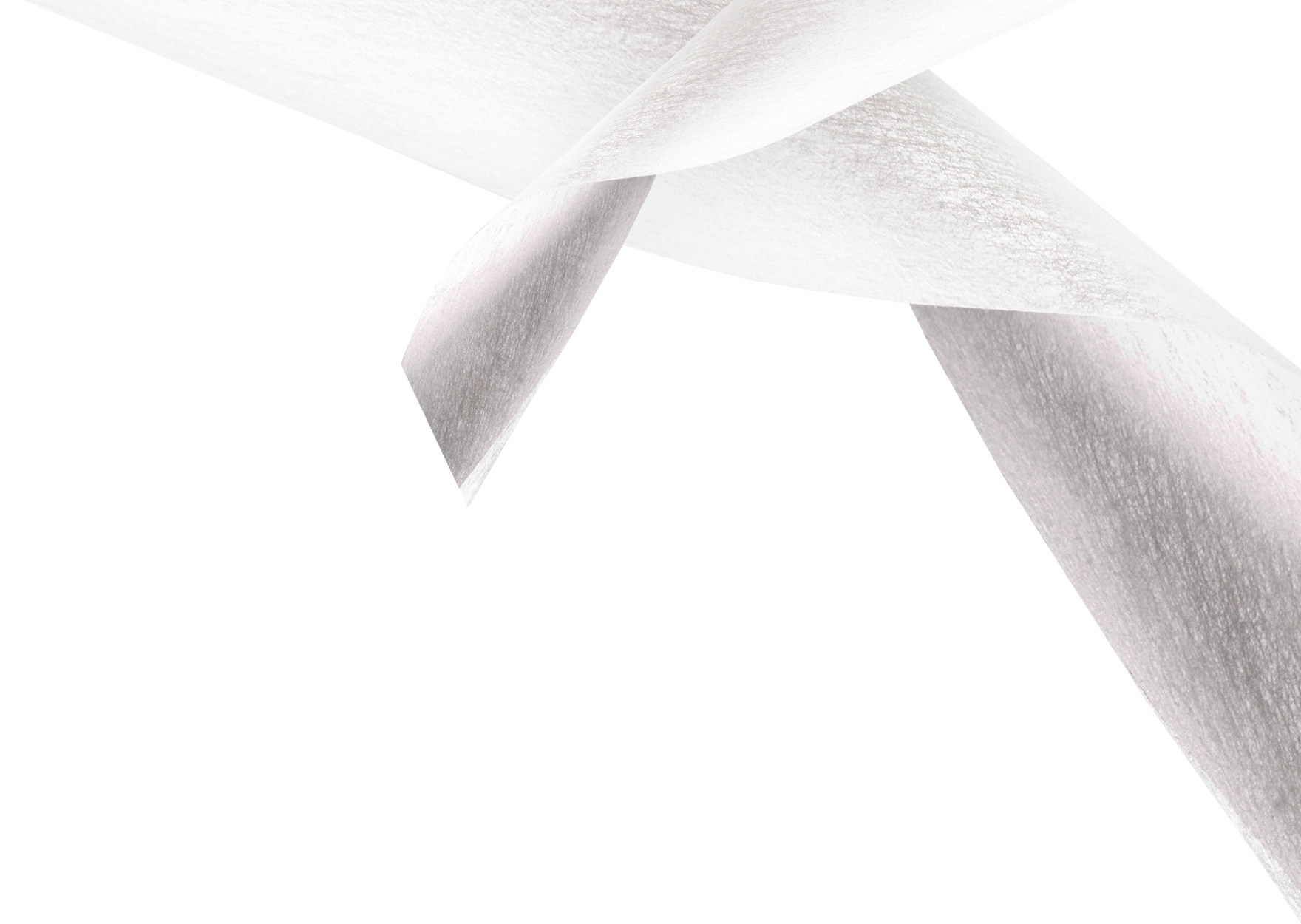
Innovation – it’s in our DNA.
While the potential of SNUS and modern oral pouches is vast, we have already invested in groundbreaking product technology to ensure you have the ultimate fabrics for your application.
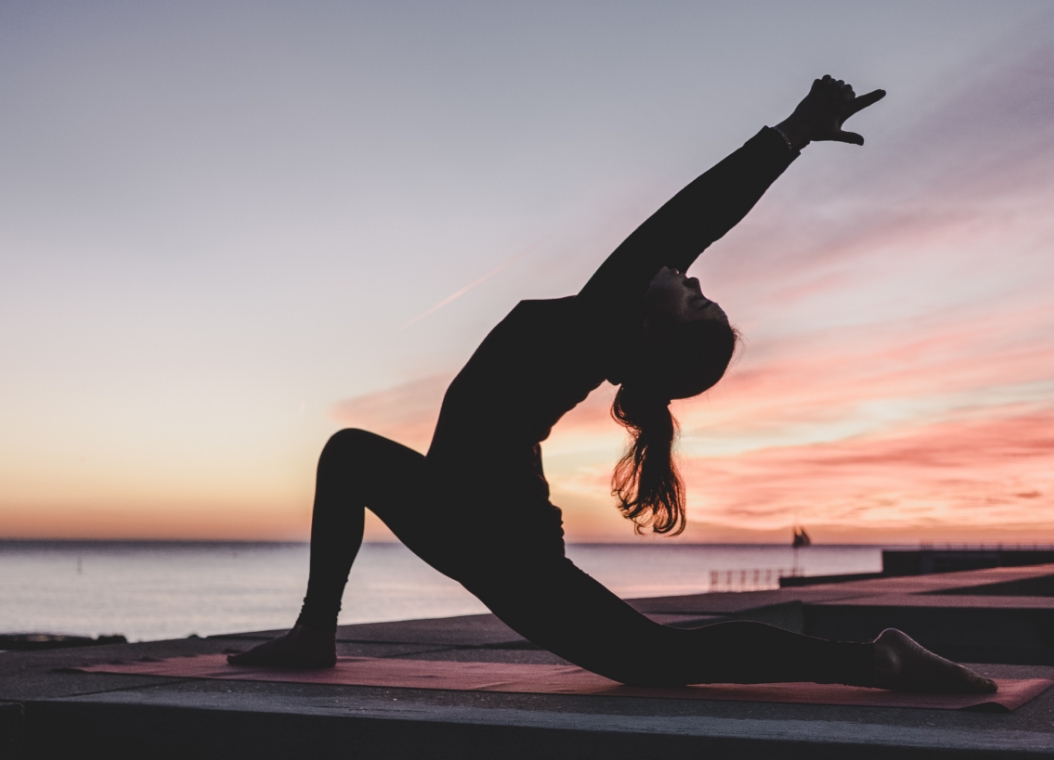
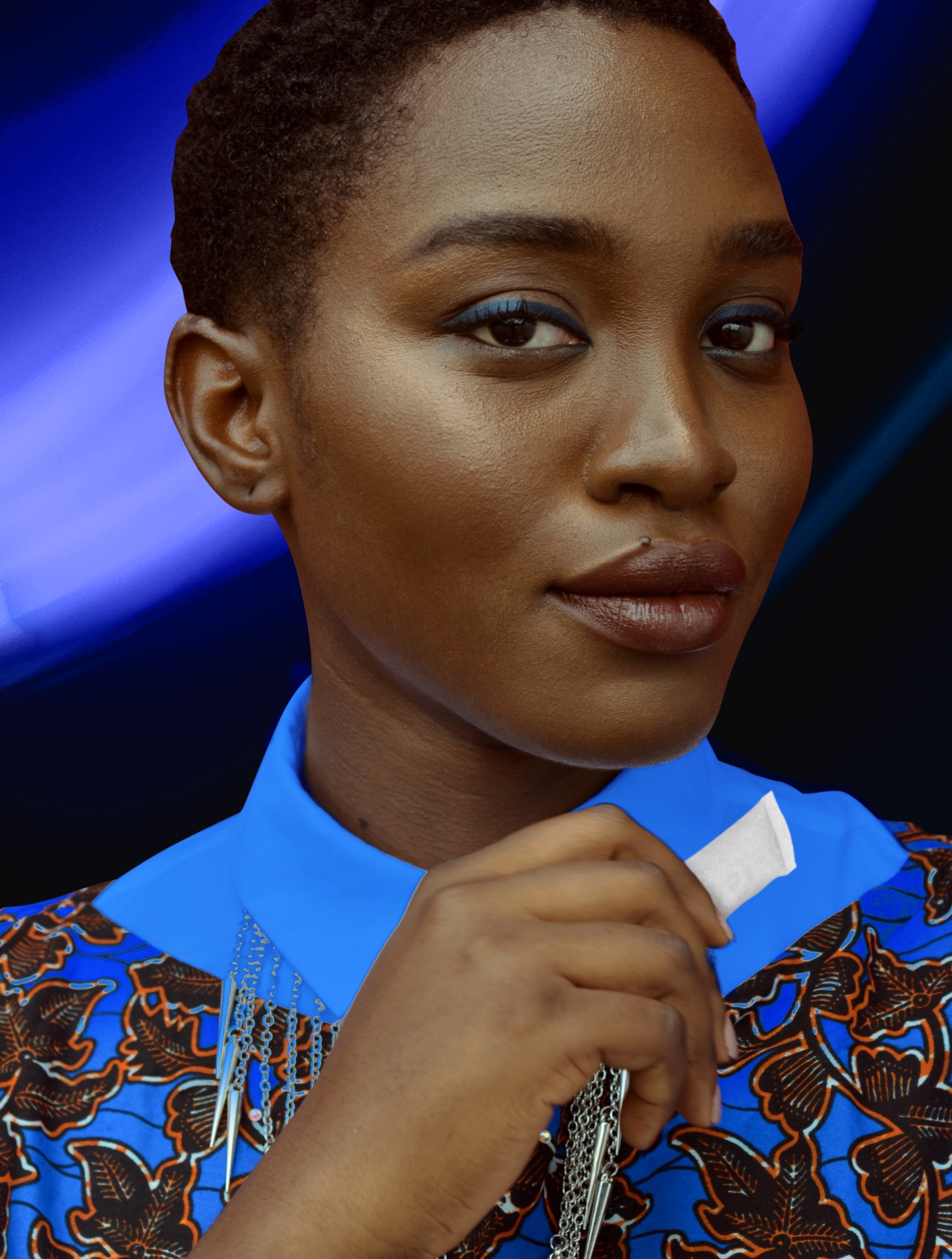
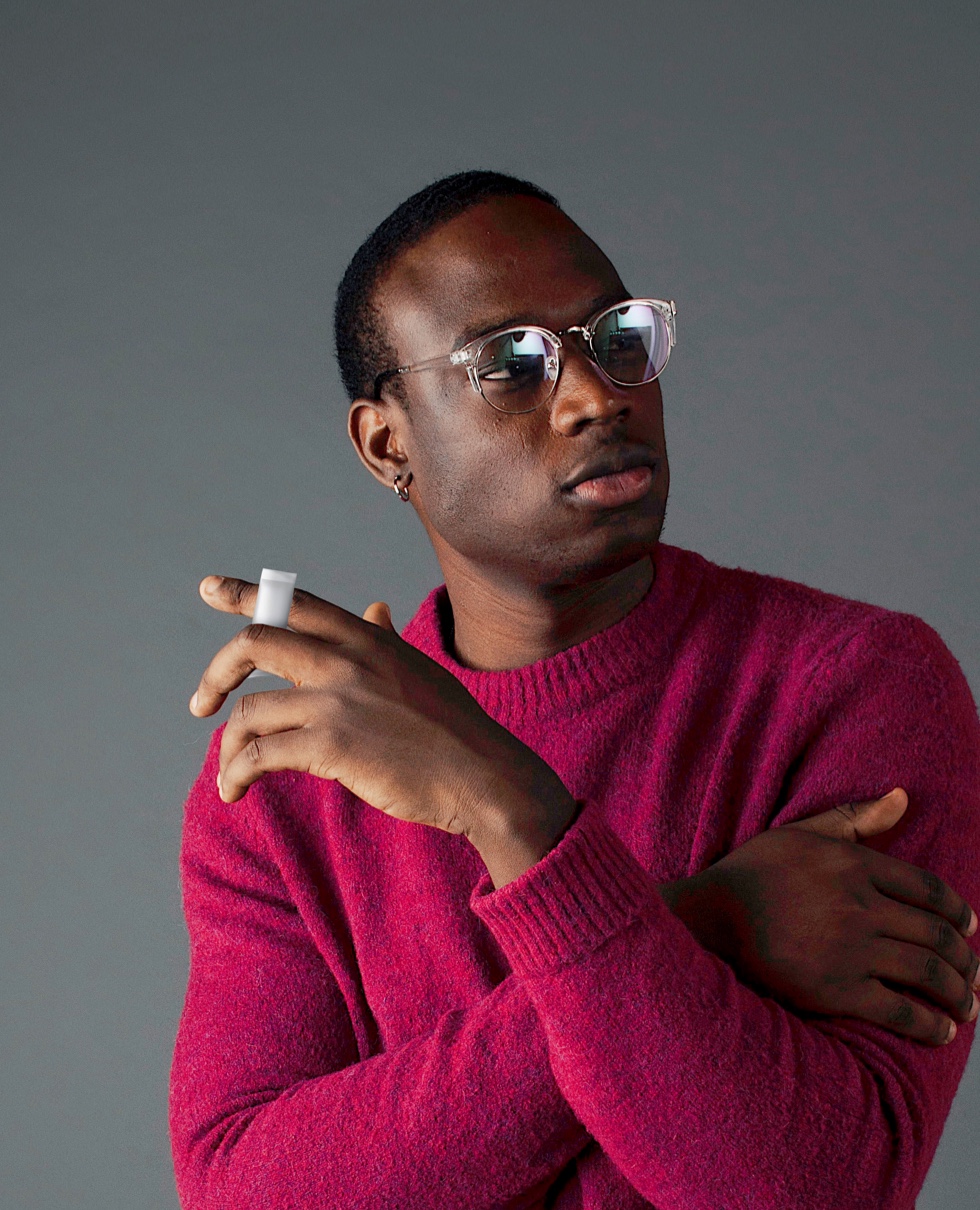
Ingenious innovations
01
Chewable Fabric
We develop game-changing, highly regulated fabrics that both particulate and facilitate gaseous chemical entrapment. Our unique design is the basis for a range of performance functionality variants.
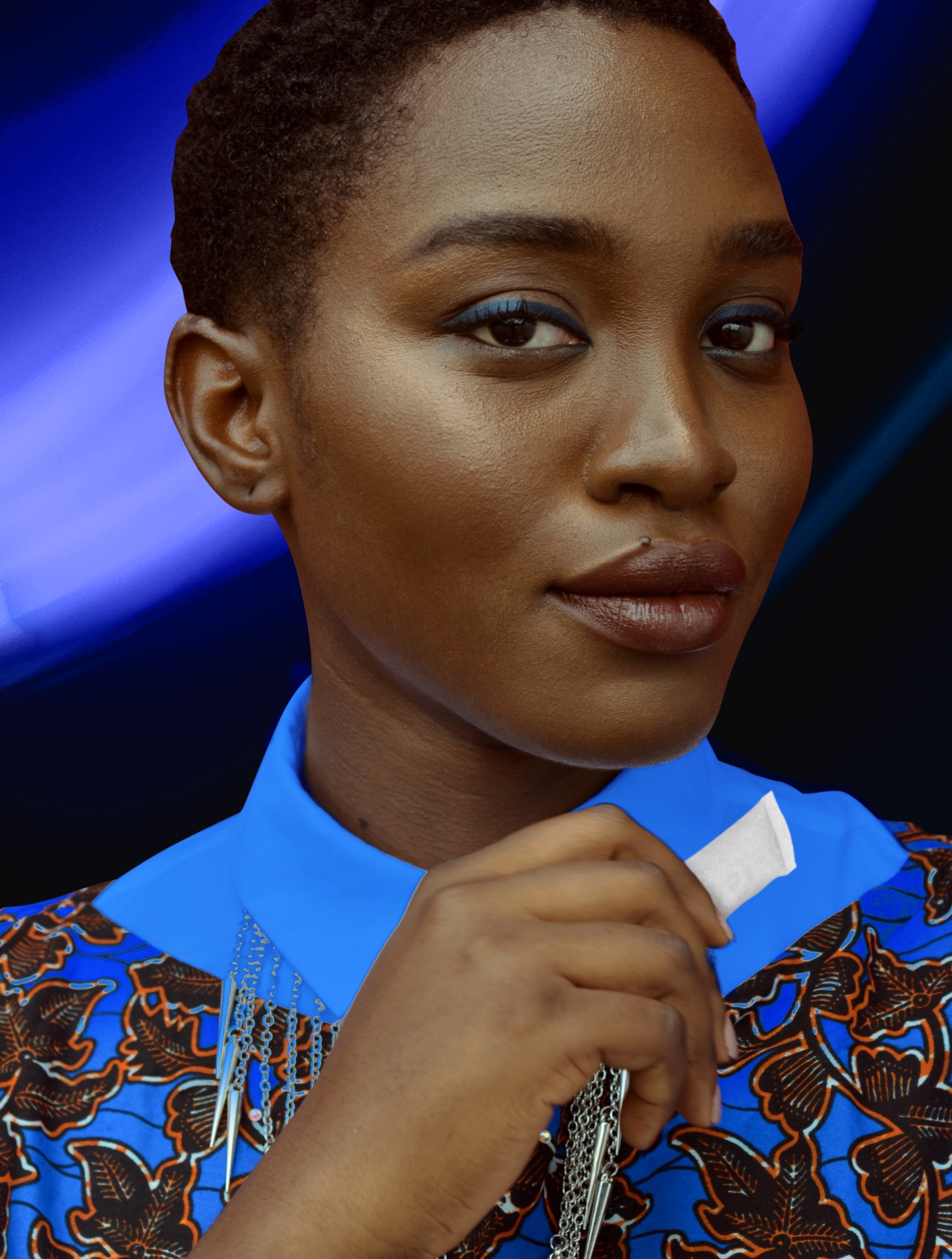
02
Chemical & Thermal Bonding
We have adapted our chemical engineering expertise to create thermally bonded modern oral pouch fabric without incorporating binders, using a ‘chembond’ process.
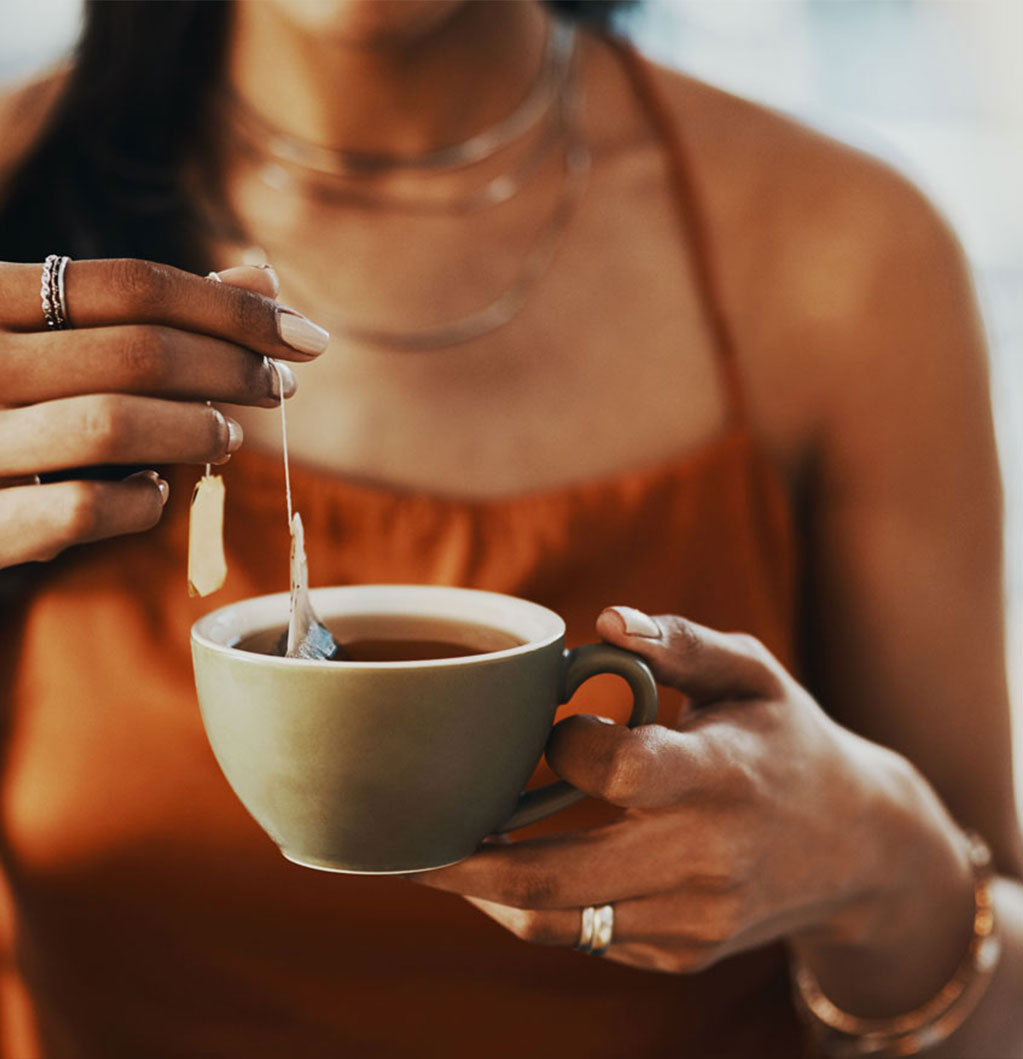
03
Chemical resistance fabric
Our specialist material can resist chemical attacks that could otherwise deteriorate the integrity of your product. Such resistance stability to additives include softening agents, flavourings and humectants.
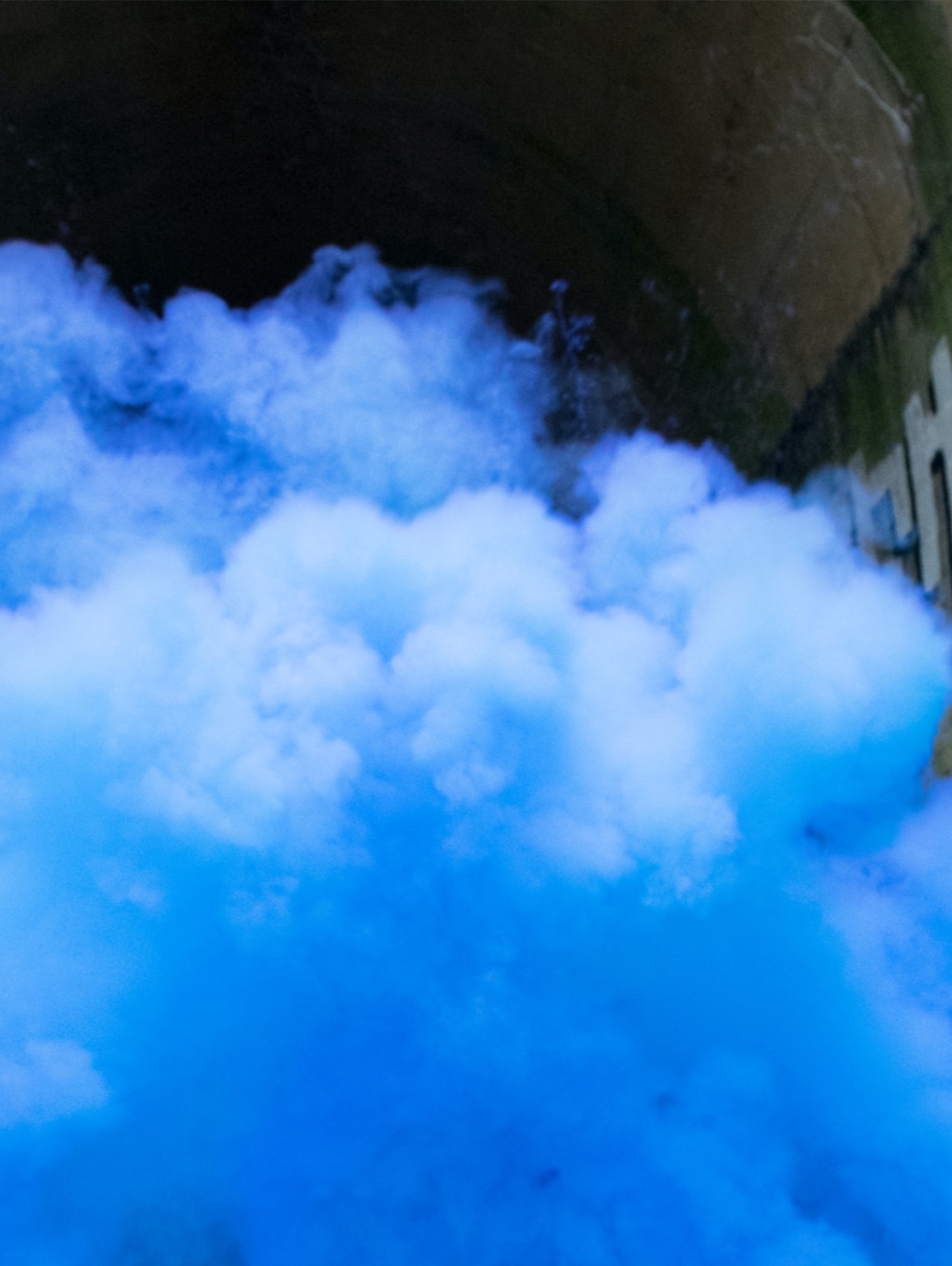
04
Controlled flavour release fabric
Our scientists at Nonwovenn have configured a revolutionary fabric that controls the flow-rate of your active ingredient. This means your users can enjoy more, or less, of your painstakingly perfected flavour.
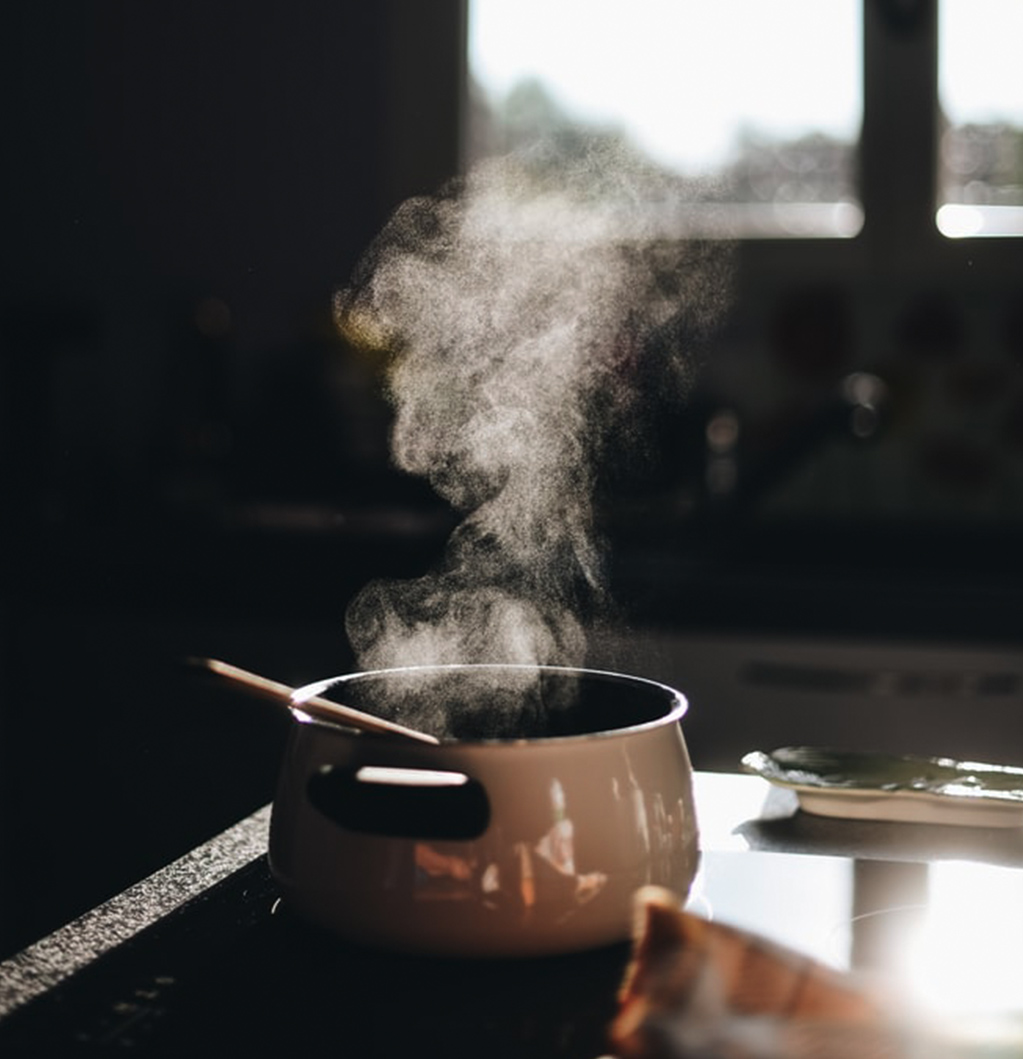
05
Biodegradable fabric
Our biodegradable fabric is constructed entirely from renewable biomass sources, such as vegetable fats and oils, cornstarch, and cellulosic materials. Biodegradable technology (viscose/PLA/PVOH/PBS/bamboo, binders, and natural bast fibres (including hemp, ramie, jute, flax, kenaf & nettle).
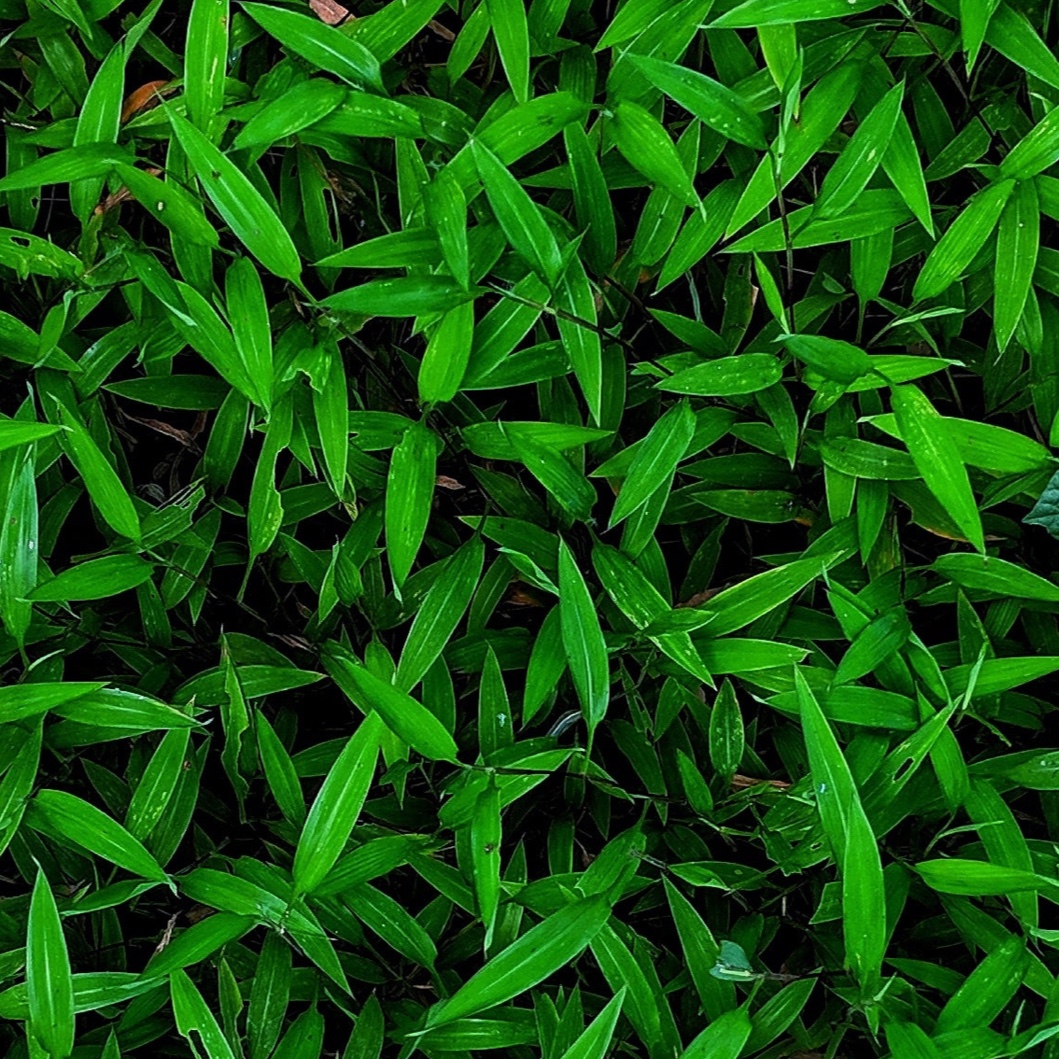
06
Lozenge products
Our nonwoven lozenge product provides a secure casing for your flavoured contents. When the user chews the lozenge, the flavours are gently released to enhance the experience.
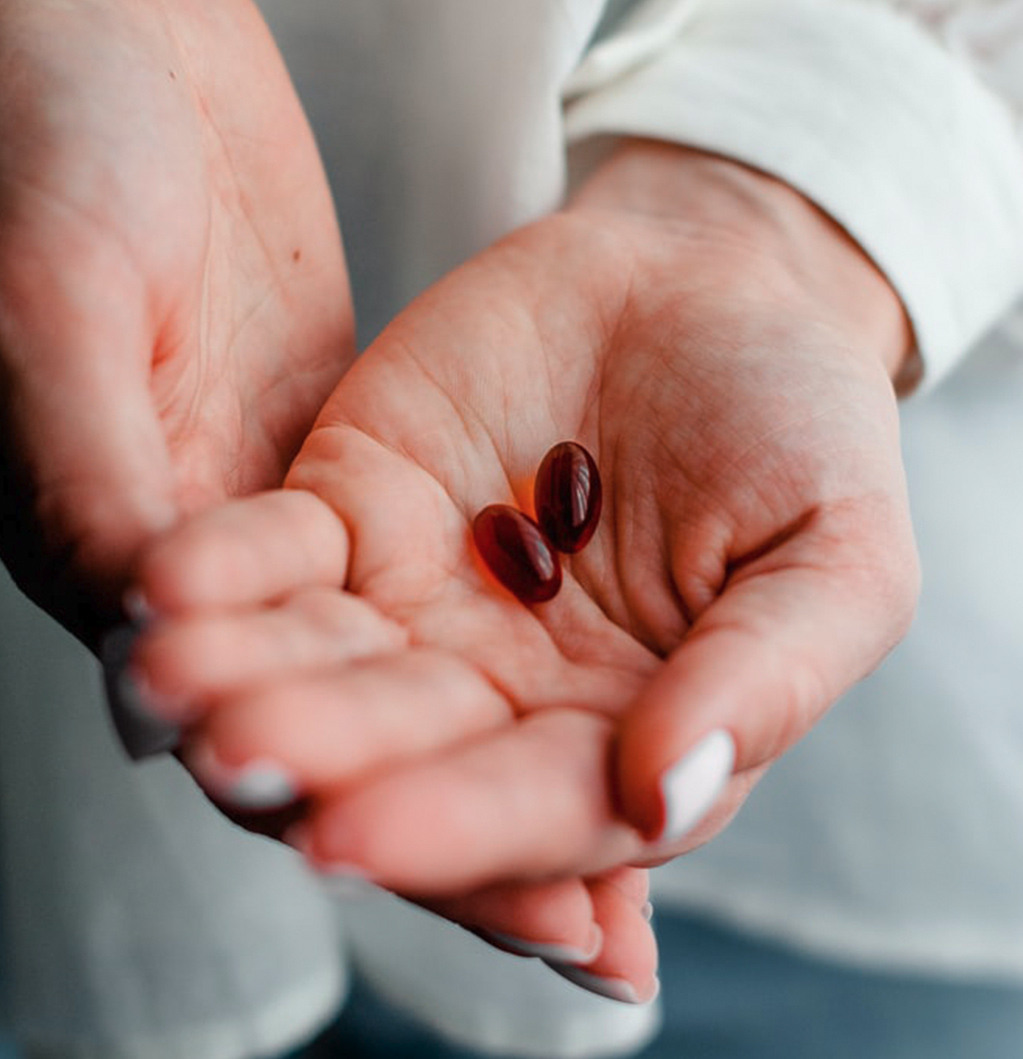
07
Lyocell-based fabric
Our sustainable, lyocell-based fabric can withstand manipulation in your end-user’s mouth when chewed – all while maintaining a desirable oral feel.
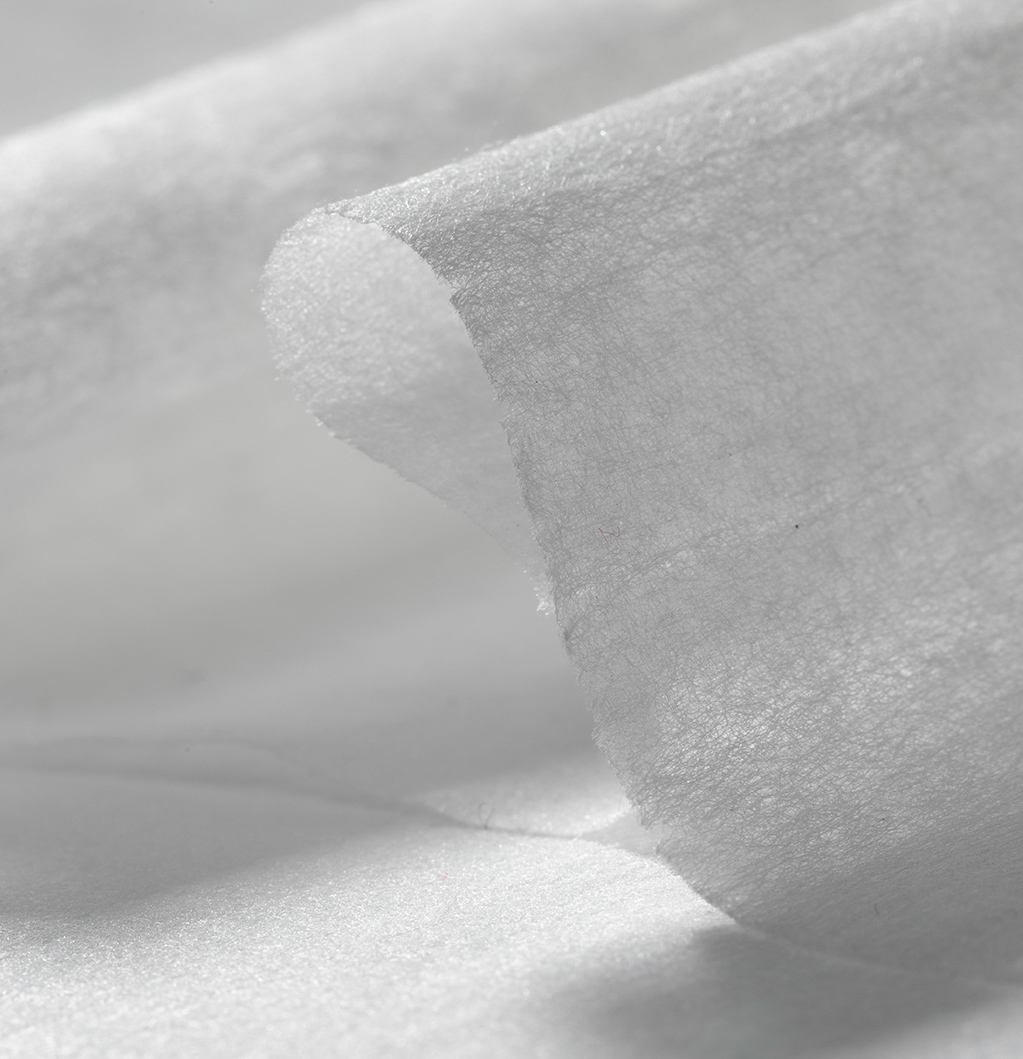
08
Fibres and finishing agents
We have carefully compiled a selection of fibres and binders that influence the fluid transport of novel nonwovens.
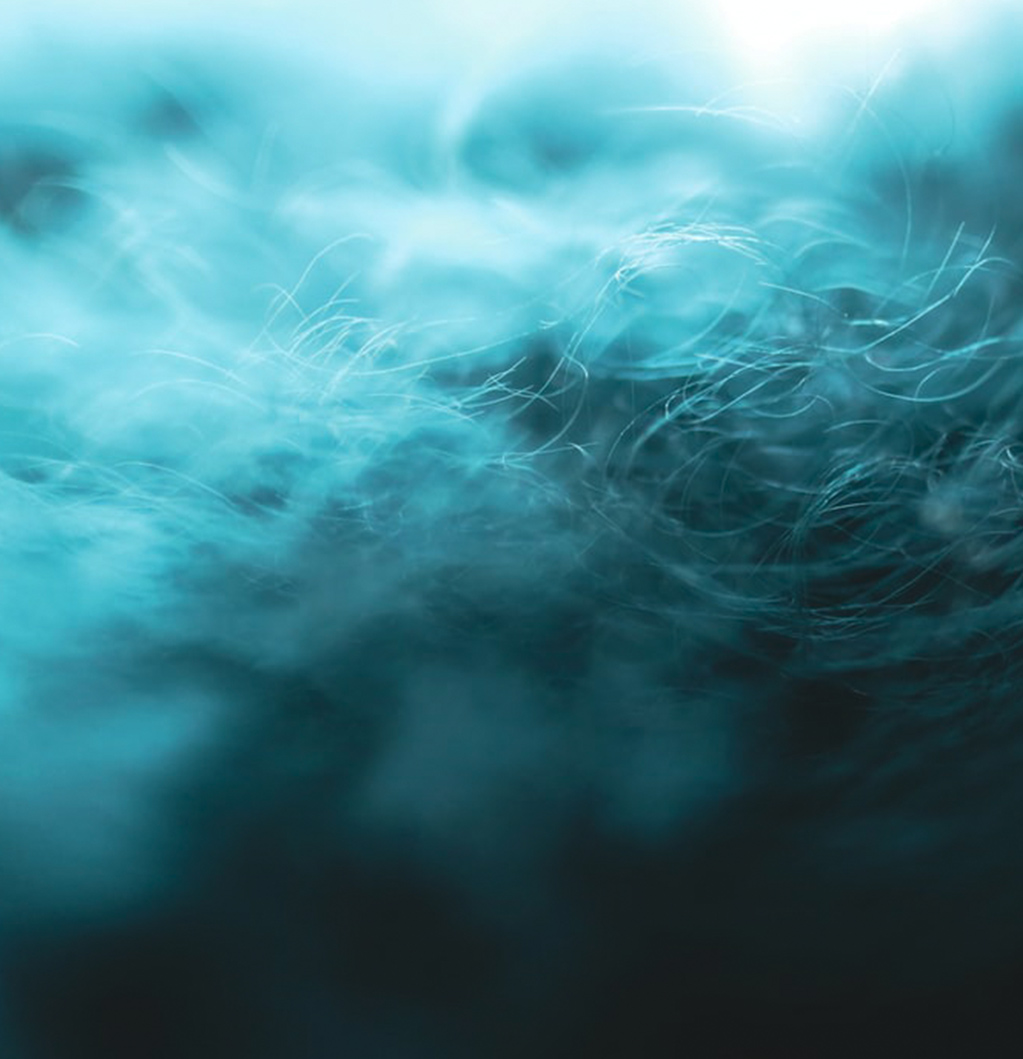
Our pouch partners
Our leading technical partners provide vital analysis capabilities and expertise on key performance measurements.
01
MERZ – GD – Hauni – Protoco
We work closely with MERZ, GD, Hauni and Protoco to optimise our equipment and maximise our output.
02
Stickpack
Stickpack provides the equipment needed to rigorously assess pouch product properties.
03
Viking – RoPack – SidSam
We align ourselves with Viking, RoPack and SidSam to relay our technical know-how and improve the pouch manufacturing process.
Smart Technology
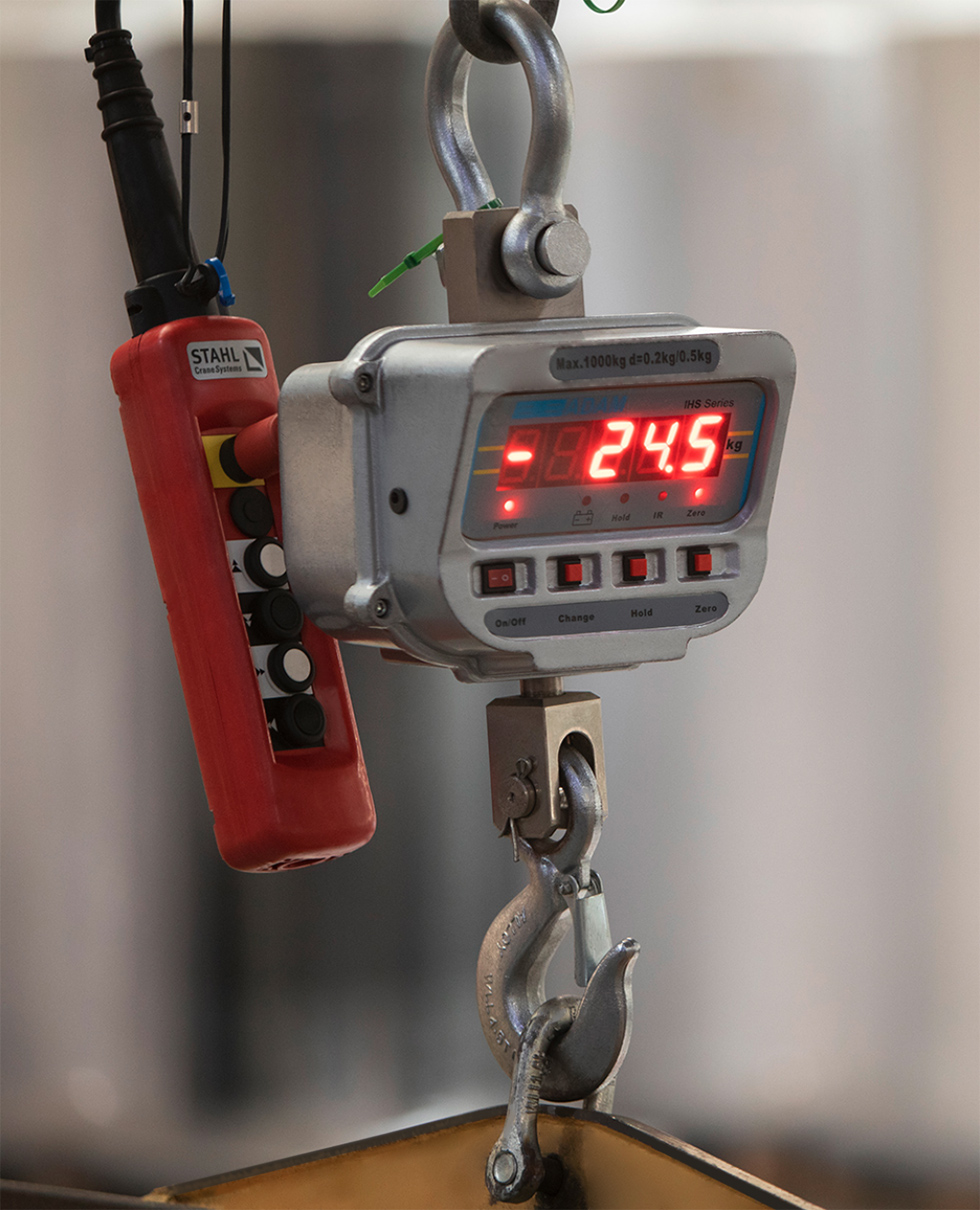
Weight reduction
We’re constantly developing lighter, technically superior fabrics that help maximise your efficiencies and minimise your costs.
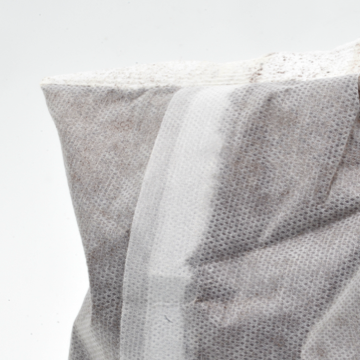
Sealable nonwovens
We have over 30 years of experience designing and developing sealable fabrics that separate all manner of products.
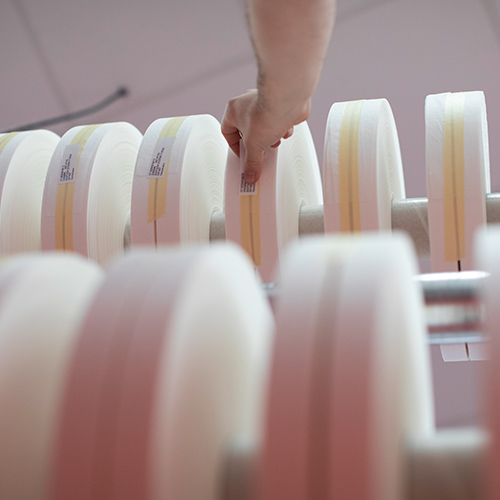
Filter papers
As pioneers in this growing field, our filter papers are the go-to solution for eliminating contaminants.
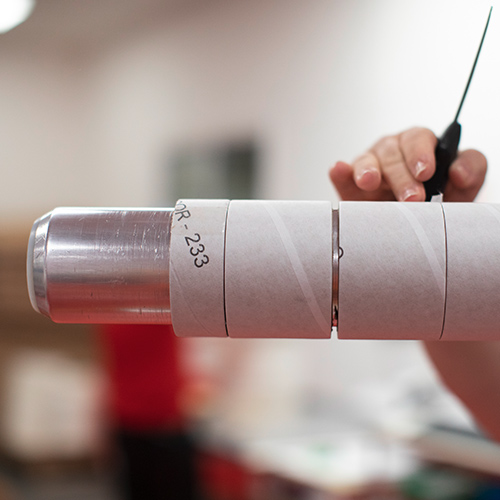
Specialist tapes
Our nonwoven tapes are painstakingly engineered to meet specific needs, from water blocking and absorbency to filtration and breathability.
Don’t just imagine a safer world, make it.
To find out more about our innovative protective solutions, get in touch.